PVD-покрытие для пластиков с высокой твердостью и стойкостью к истиранию
Naxau имеет специализированную команду по исследованию и разработке процессов нанесения покрытий для литья под давлением, с поддержкой больших данных 12 000 успешных случаев от 2 000+ известных пользователей по состоянию на 2018 год. Мы знакомы с процессом литья изделий под давлением и понимаем влияние распределения температуры пластика, скорости впрыска, давления, положения и других параметров процесса на качество покрытия, поэтому мы можем помочь клиентам решить различные проблемы литья под давлением более эффективно.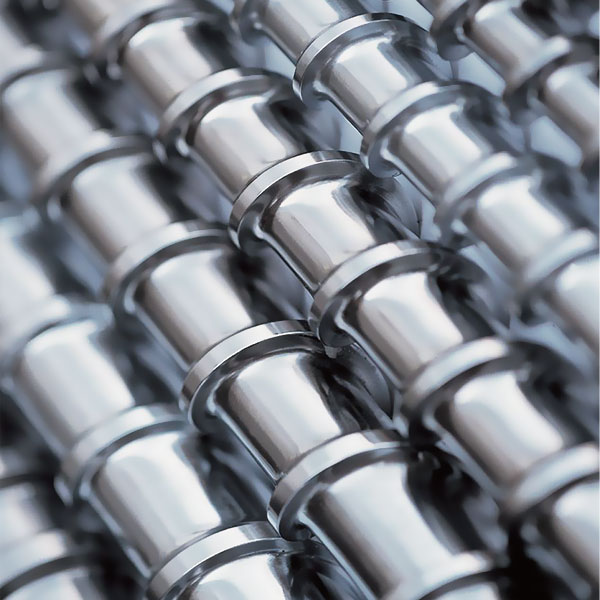
Высокоточный антиадгезив Решения для нанесения покрытий
Твердость поверхности: 2000HV
Толщина покрытия: 0,01-0,02 мм
Устойчивость к истиранию: ★★★★
Устойчивость к коррозии: ★★★★★
Антипригарная способность: ★★★★
Применимые условия работы: высокая скорость, высокое давление, липкий материал; для прозрачных оптических изделий, всех видов линз, световодных пластин и т.д.; обычно используется пластик для оптических изделий: PMMA, PC, COC, COP, CR-39 и т.д.;
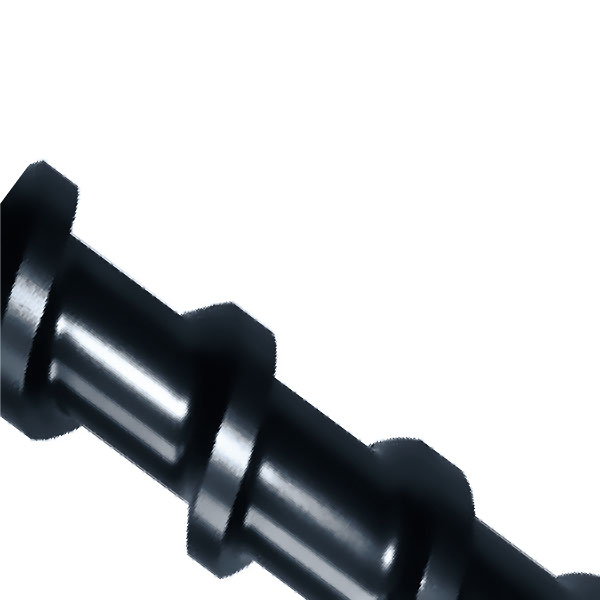
Высокая твердость стекловолокна углеродного волокна Решения для нанесения покрытий
Твердость поверхности: 3500HV
Толщина покрытия: 0,005-0,07 мм
Устойчивость к истиранию: ★★★★★
Устойчивость к коррозии: ★★★
Применимые условия: стекловолокно, инженерные пластмассы, содержащие 70% и ниже; углеродное волокно, содержание 50% и ниже; такие как: PA, PC, PBT, PPS, PAR, PEI, PEEK и т.д.
многослойная мембранная структура Более длительный срок службы
Запатентованная технология SPARK Nano
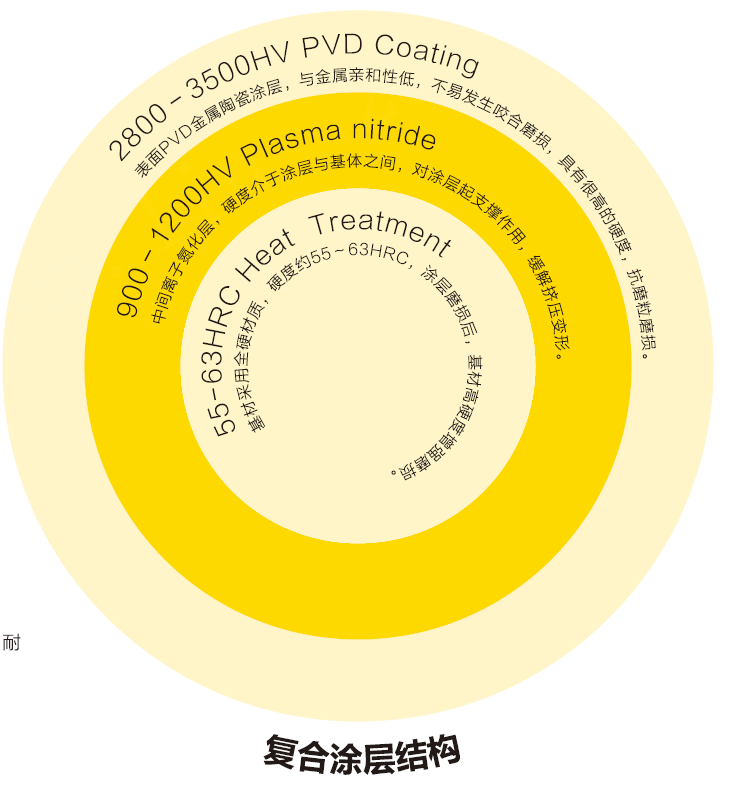
Компания Naxau использует комбинацию вакуумного азотирования и процесса обработки поверхности титанового покрытия PVD, который не только обеспечивает поддержку поверхности субстрата для высокотвердого слоя титанового покрытия, но и реализует переход напряжения от мягкого к твердому. Наси многослойная пленка, более плотная решетчатая структура; и отсутствие трещин более устойчивы к коррозии.
Вопросы: Испытательное оборудование: тестер трения и износа "штифт на диске" (тип SFT-2M)
Скорость вращения диска: 150 об/мин Общий ход: 163 м.
Вопросы: Испытательная нагрузка: постоянная нагрузка 470 г.
Пункт повестки дня: ТОКИО-ЯПОНИЯ P600
▇ Сталь и твердость: SKD61, твердость 52HRC
▇ Толщина покрытия: 3,8 мм, твердость 2200HV
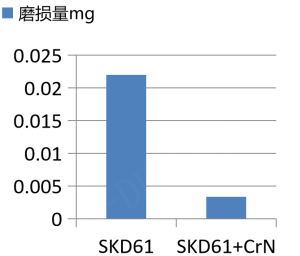
Испытание антилипкого материала - угол смачивания при высокой температуре
Испытание антиадгезионного материала
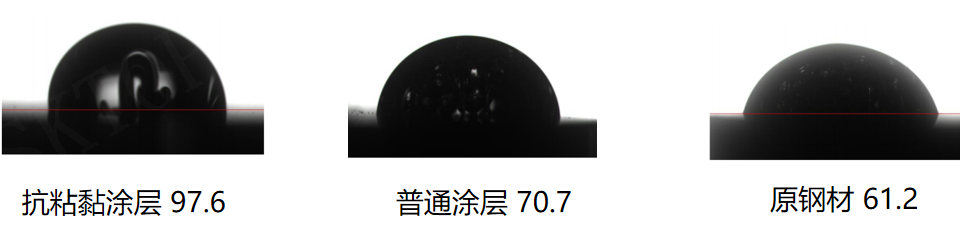
Условия испытаний:
Пункт повестки дня: ПК AD5503 (Teijin)
Вопросы для рассмотрения: Антиадгезионное покрытие Nashion, обычное покрытие, образец без покрытия
▇ Шероховатость поверхности образца: Ra 0.2um
▇ Температура: 300°C
Типичные типы покрытий для литья под давлением
Тип | Твердость: HV | Толщина пленки: мкм | Температура антиоксидантов | Коэффициент трения | Цвет | Подходит для обработки материалов |
CrN | 1800-2200 | 10-20 | 700 | 0.4 | Пепельно-серый | Применяется для прозрачных оптических изделий, всех видов линз, световодных пластин и т.д.; широко используемые пластики для оптических изделий: PMMA, PC, COC, COP, CR-39 и т.д. |
CrAl+ | 3000-3500 | 5-7 | 1000 | 0.5 | Темно-серый | Тип стекловолокна, инженерные пластмассы, содержащие 70% или менее; тип углеродного волокна, содержащий 50% или менее; К таким пластикам относятся PA, PC, PBT, PPS, PAR, PEI, PEEK и др. |
DLC | 2000 | 1-3 | 350 | 0.1 | Blackl | Тип литьевой формы; коррозионная стойкость, антиадгезия; |
Сравнение свойств DLC и Ta-C
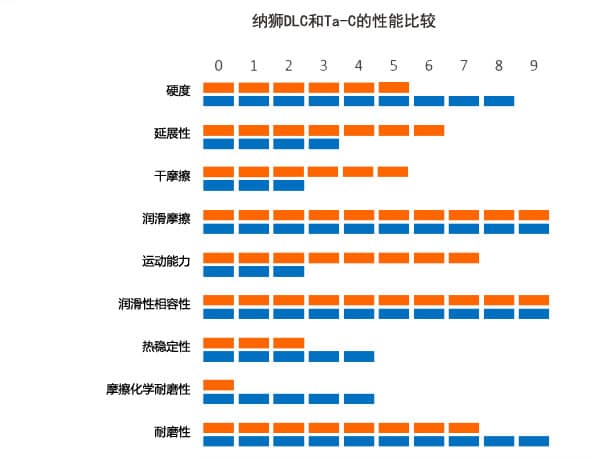

Применение пресс-форм для литья под давлением с PVD покрытием
Инжекционные пресс-формы - часто задаваемые вопросы о нанесении винтового покрытия
Вопрос о том, использовать ли хромирование или PVD титановое покрытие для шнеков литья под давлением, должен решаться в зависимости от конкретных сценариев применения, требований к производительности, стоимости и экологических требований. В настоящее время, литьевые винты в основном покрыты, в то время как технология PVD в основном используется для литья под давлением с высоким содержанием углеродного волокна, стекловолокна и других твердых износостойких материалов.PVD титанового покрытия в применении литьевых винтов имеют много ограничений