Composite Collector #
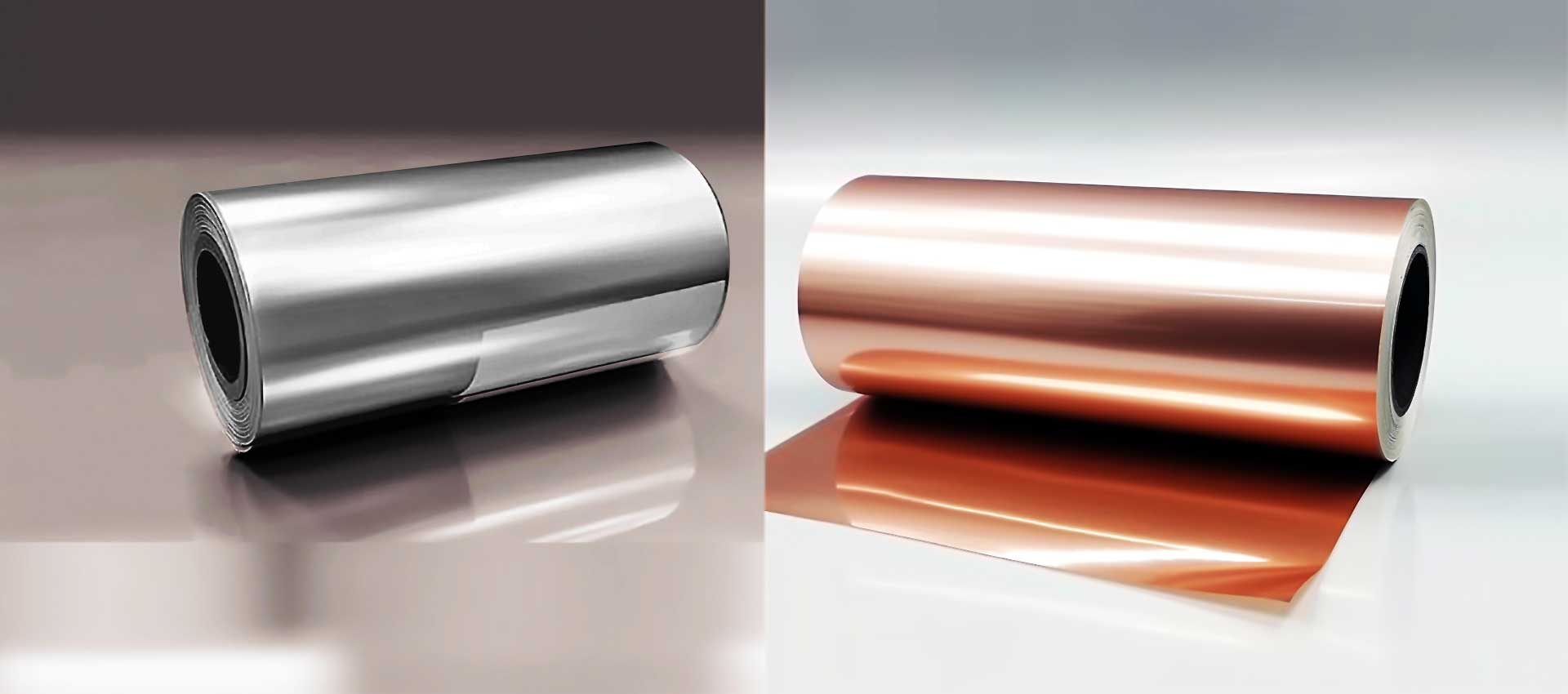
Composite collector can provide higher safety, higher specific energy, lower cost of lithium-ion battery technology direction, with good insulation, low density, low cost of PET, Pi and other polymer materials as the substrate of the composite collector came into being. Advantages of composite collector:
- High safety : Avoiding the risk of internal short circuit and improving battery safety.
- High energy density: weight reduction 50%-80%, energy density increase 5%-10%
- Longer life: more uniform surface, increased cycle life 5%
01 Sandwich composite structure #
The composite collector is a “sandwich” structure, with a polymer layer of PET, PI, PP, etc. in the middle and a metal conductive layer of copper or aluminum on both sides. The polymer base layer provides good flexibility and mechanical stability, and can adapt to the volume change of the battery in the charging and discharging process. The conductive layer is responsible for electron conduction to ensure the smooth transfer of electrons in the electrode reaction. This unique structural design makes the performance of composite collectors in lithium batteries very different from that of traditional collectors, laying the foundation for the improvement of lithium battery performance.
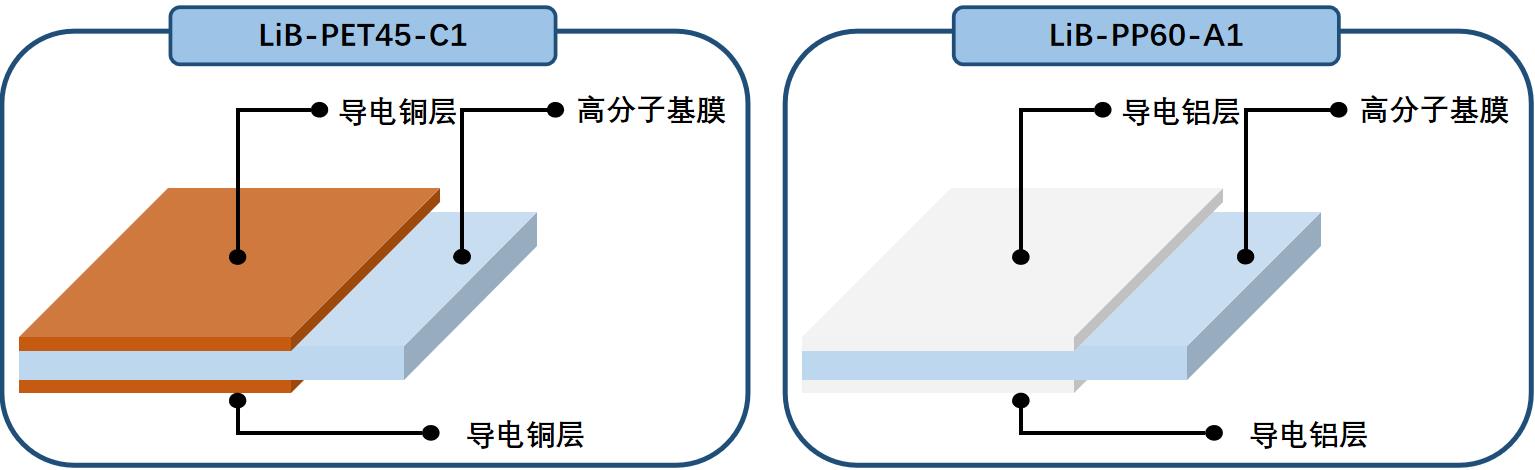
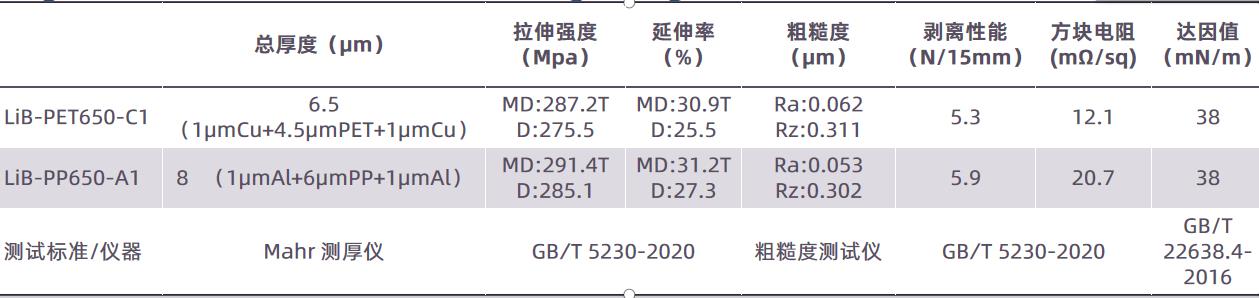
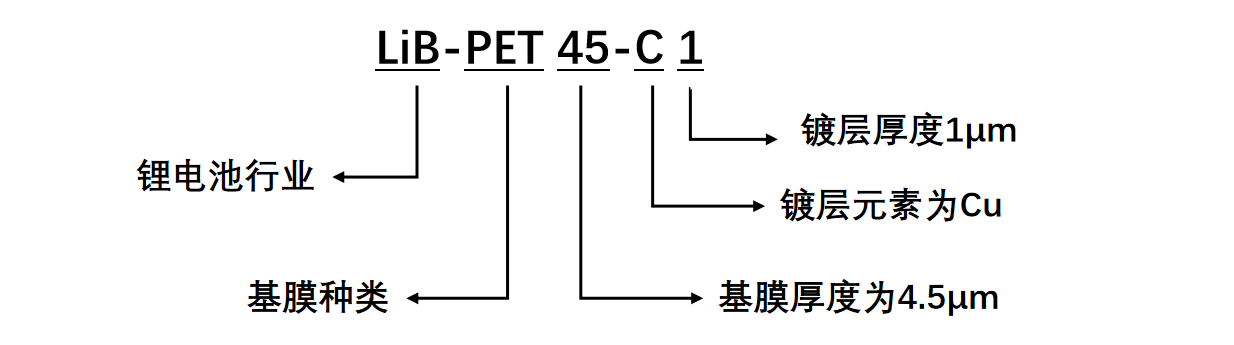
02 Comparison of the performance of commonly used substrates for composite fluid collectors #
Polymer diaphragm substrates | PET | PP | PI |
Materials | polyethylene terephthalate | polypropylene | polyimide |
Diaphragm temperature resistance | Above 260°C | 160℃左右 | Above 360°C |
Diaphragm chemical stability | Polar material, easy to produce chemical bonding with metal substances, strong bonding of plating layer | Non-polar material; can be eroded by strong acids such as concentrated sulfuric acid and concentrated nitric acid; | High thermal and chemical stability |
Polymer Film Disadvantages | Degradability: PET is prone to degradation at the negative end of lithium batteries. | Higher machining difficulty, small process window | Cost: PI is more expensive and cannot be mass-produced for the time being. |
Polymer Film Cost | About 0.75 million RMB/ton | About 0.79 million RMB / ton, but the depreciation cost of production equipment is higher than PET | Higher cost, unable to mass produce for the time being |
Diaphragm Application Scenarios | Scenarios Energy Storage Applications; Anode Materials | power cell | – |
03 Composite Copper Foil Preparation Process #
Composite copper foil is a new application in the lithium industry, but its essence is to metallize/conduct the non-metallic film. Composite copper foil has been widely used in electromagnetic shielding materials, ITO coating, copper cladding board and other industries.
The production process of composite copper foils mainly includes one-step, two-step and three-step methods. The composite copper foil preparation processes currently used by the industry include one-step (chemical deposition, magnetron sputtering, vapor deposition), two-step (magnetron sputtering + aqueous plating) and three-step (magnetron sputtering + vapor deposition + aqueous plating).
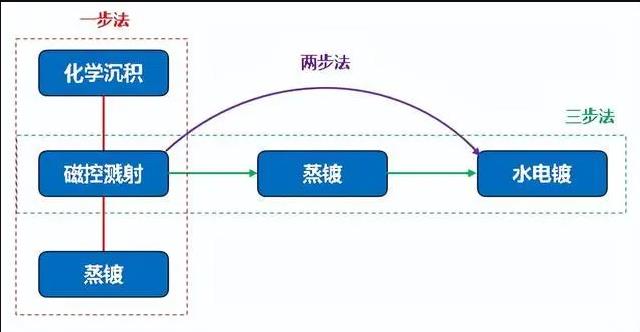
Naxau composite copper foil and composite aluminum foil are JVAD one-step vacuum coating process.
04 Naxau One-step JVAD vacuum coating #
One-step preparation of composite copper foils can be accomplished by repeated magnetron sputtering or evaporation plating to finally deposit the copper layer to 1-2um, but due to the high price of the equipment and the slow reaction rate, if only one-step preparation of composite copper foils is done by magnetron sputtering or evaporation plating, the capacity of the equipment will be drastically reduced and the cost of manufacturing will skyrocket. NanoShield JVAD coating technology combines the high bonding power of sputtering coating and the fast deposition of evaporation plating, and is capable of rapid double-sided deposition of highly dense metal films.
Compared to other multi-step methods, Nasi’s one-step process is less expensive, less prone to wrinkles and has higher yields; the metal film is more uniform and has fewer surface defects. In addition, the one-step process can prepare wider metalization, the current maximum width of 1650mm.
- High film thickness uniformity
In a vacuum environment, the trajectory of the particles is more regular, and the one-step method allows for highly uniform deposition on a polymer 0.65mm ultra-thin substrate, resulting in the formation of a conductive film layer of uniform thickness, which improves the battery’s charging and discharging efficiency and consistency. - High purity and density
The vacuum environment greatly reduces impurities. Moreover, JVAD high-energy deposition technology is capable of depositing a highly dense metal film, which further enhances the energy utilization of lithium batteries. - No damage to film substrate
Mild process conditions do not subject the polymer to thermal distortion, degradation, etc. Denser metal film reduces electrolyte attack on the substrate
05 Other Composite Collector Common Preparation Processes #
Common traditional copper foil process: calendering method, electrolytic method. Traditional aluminum foil process: calendering method, evaporation method.